What is a handling process?
The handling process refers to the process whereby a robot hand, etc., grasps a product on the production line.
The key point in selecting the actuator required for the handling process is "whether or not it can securely grip the workpiece without destroying it and without allowing it to fall during the conveying process.
Hand chucks are suited for handling workpieces that are difficult to deform because of their high force.
On the other hand, a gripper can softly grip even a deformable workpiece because its movement and force can be controlled.
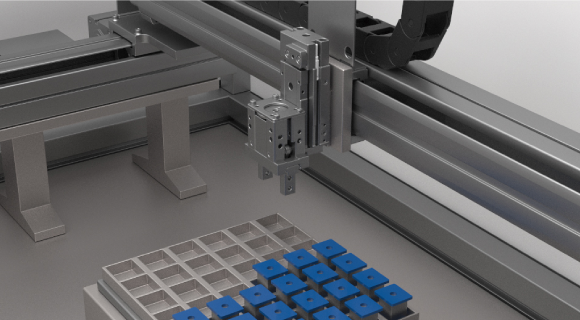
Key Points for Selection
Whether soft handling is required or not
If the workpiece is a hard material such as metal or resin and will not be deformed even if strongly gripped,
a hand chuck is recommended.
If the workpiece is made of easily deformable materials such as rubber or silicon,
a gripper that can softly grasp the workpiece is recommended.
If a soft hand is not required Hand chuck
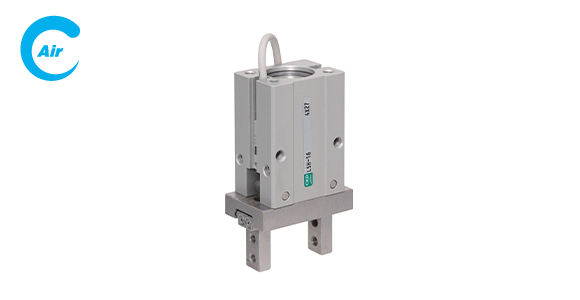
If a soft hand is required Gripper
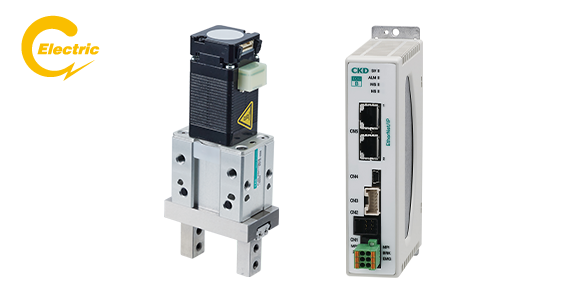
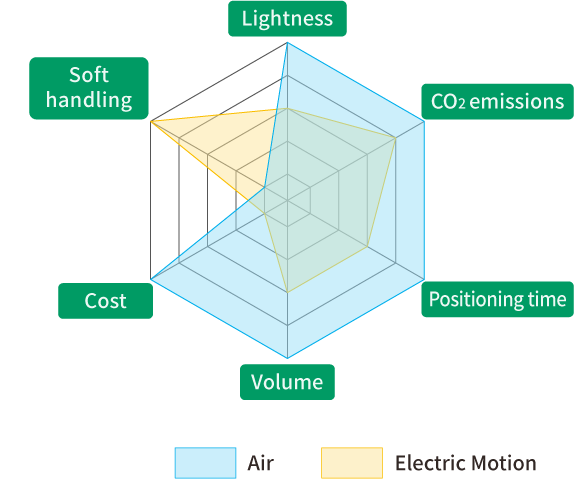
Basically, hand-chucks are recommended
Basically, the lighter the hand, the better.
A light hand can reduce the load on the transport actuator and robot, and its size can also be reduced.
For example, in the case of our product, the LSH-A20-HP1 hand chuck weighs 295g and the FLSH-20G gripper weighs 380g.
For the same gripping force, we recommend the air type with lighter weight.
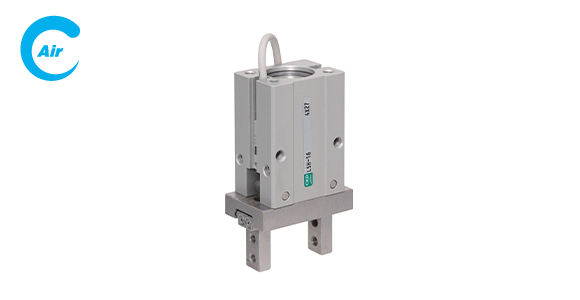
CKD hand chucks are wide in variations and
are easy to select.
Thin parallel hand
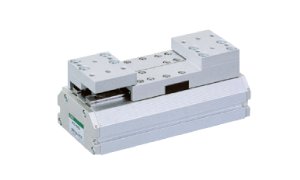
Wide parallel hand
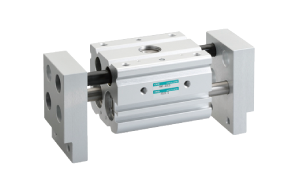
3-way chuck
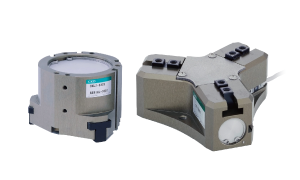
Grippers are required for soft hands
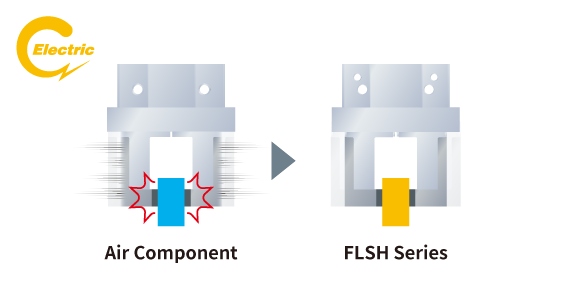
For fragile workpieces, it is recommended to use a gripper with variable speed to avoid impact and variable gripping force to match the workpiece for gentle gripping.
CKD's FLSH expands your options
CKD's FLSH Series is compatible with the LSH-HP1 air cylinder for easy replacement. It also has a long stroke and can handle a wide variety of workpieces with multi-point stop.
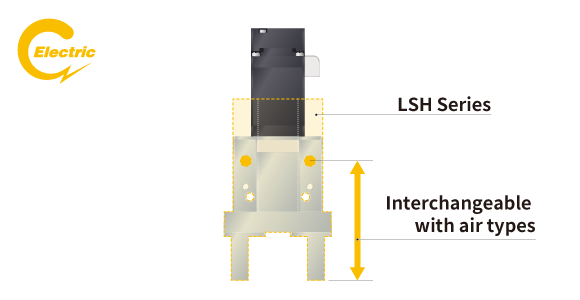
Comparison of Hand Chuck and Gripper
Let's compare the cost and performance of actual CKD hand chuck and gripper models.
Model No. to compare
Hand chuck
LSH-A20D1N-F2H-D-HP1
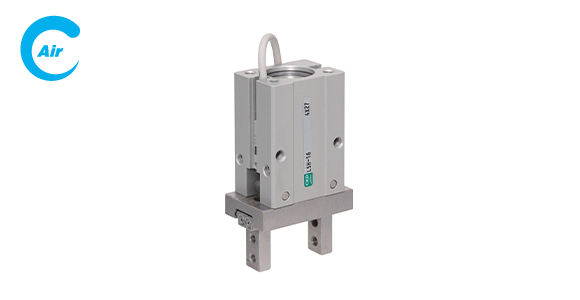
Comparison conditions
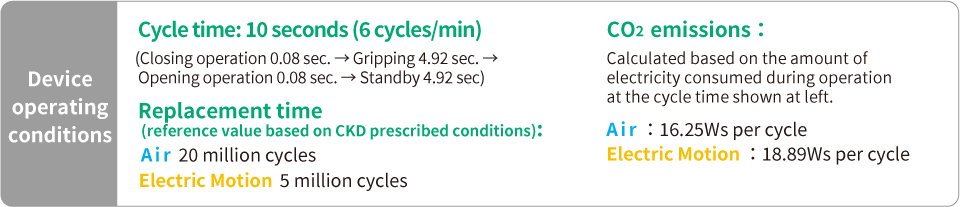
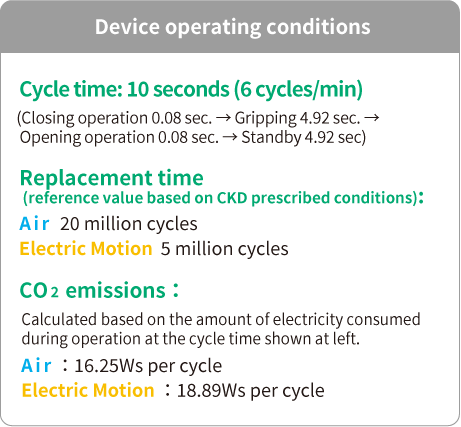

Comparison by Cost
If the high-durability Component LSH-HP1 Series is used, the frequency the air component is replaced is reduced, enabling cost reduction.
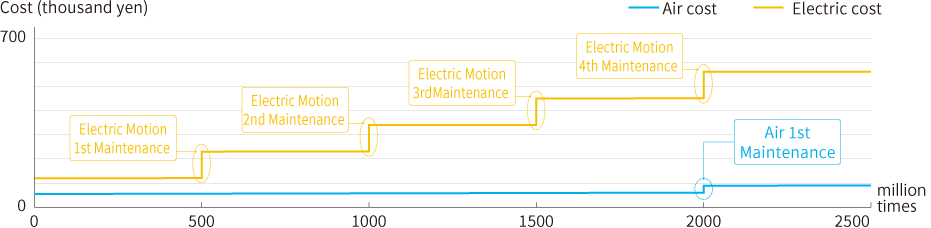
■ Calculation of costs Initial product price, product or parts price at the time of replacement, and electricity cost during operation
Electricity cost during operation: 22 yen per 1kwh.
Air is calculated by converting air consumption into electric power and combining it with the electric power consumption of solenoid valves and cylinder switches.
Labor cost for maintenance is not included.
*Replacement time is calculated based on test data under our specified conditions and is not guaranteed.
Comparison by Actuator Dimensions
Air is more compact.
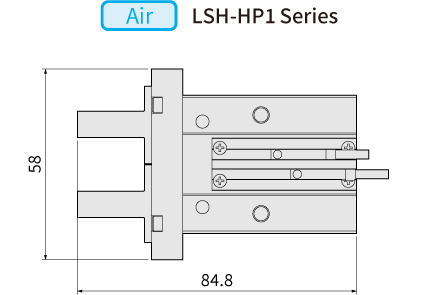
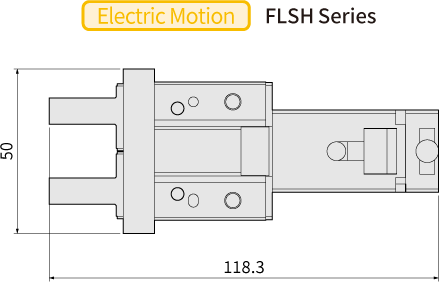
Comparison by Positioning time
The difference in travel time is small,
but the Air LSH-HP1 Series is faster when pressing judgment time is factored in.
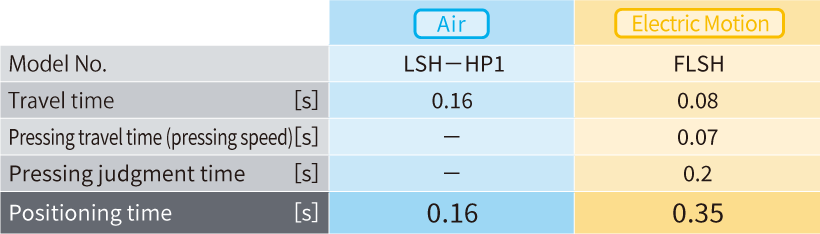
Comparison by CO2 Emissions
Air type CO2 emissions are reduced when the operating frequency is less than 9 cycles/min.
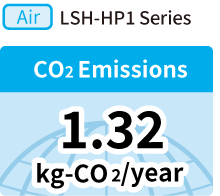
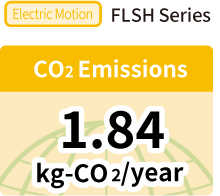
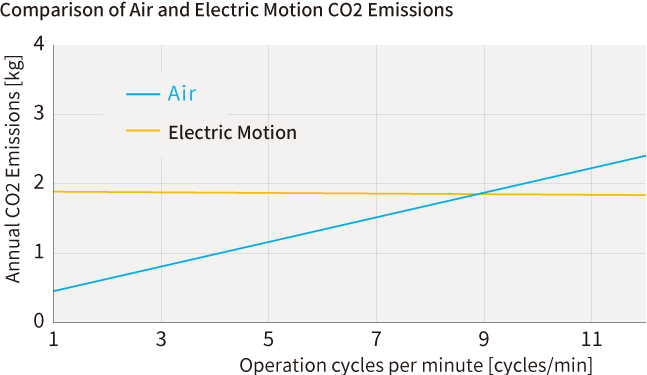
*CO2 emissions vary depending on the frequency of operation per minute.
*The longer the grasping time, the more electricity is consumed and the more CO2 emissions are generated.
■ Calculation of CO2 Emissions [Conditions] Annual operating days: 250 days Operation time: 8 hours/day Air pressure: 0.5MPa (clamp: 0.4MPa, conveying: 0.25MPa)
CO2 emissions converted from annual power consumption (kg-CO2/year) Annual electric power consumption (kWh) × 0.000406* × 1000*
*CO2 emission factor: Ministry of the Environment's publicized emission factors by electric utility, R2 fiscal year results Chubu Electric Power Mirise CO2 emission coefficient *1000:kg conversion
Air is calculated by converting air consumption into electric energy and adding the power consumption of solenoid valves and cylinder switches.
CKD Products
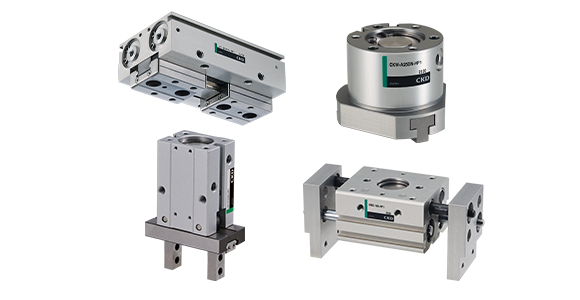
We offer a wide variety of actuators for transport and lightweight hands that can reduce the load on the robot.
Hand / Chuck
Click here for product information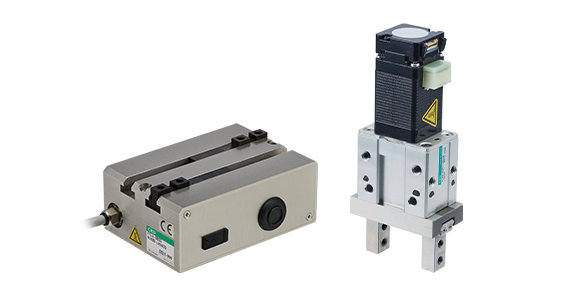
Electric actuators can control movement and force, allowing soft gripping of even deformable workpieces. Reduces workpiece damage.
Contact CKD for product selection
We respond to a wide range of needs, from product proposals to support, based on customer requests.
Please feel free to contact us if you have any problems in selecting an actuator.
Recommended drive method by process
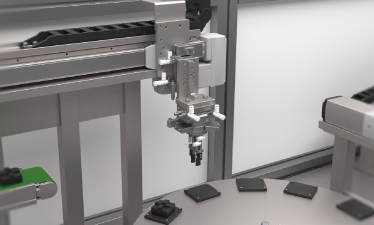
Conveying Process
Electric actuators are recommended if you want to increase positioning accuracy, while air cylinders are recommended if you want to expand the range of payload coverage.
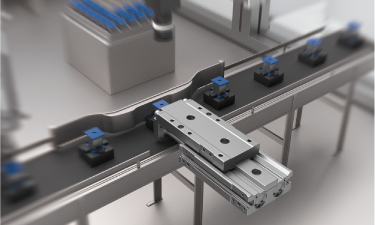
Clamping Process
The air cylinder is recommended for quick operation, and the electric actuator is recommended for shockless clamping
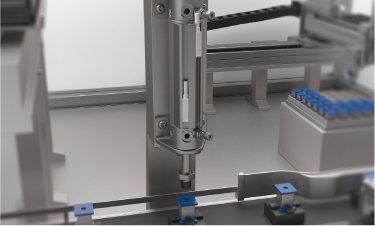
Press Fitting Process
Air cylinders are recommended for their small size and high pressing force, electric actuators are recommended for their press fitting control.
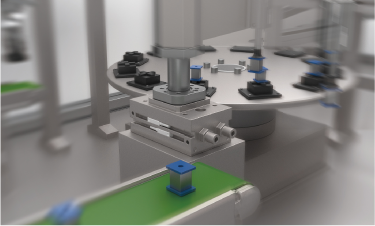
Oscillating Process
Air cylinders are recommended for their high-speed movement, and electric actuators are recommended for positioning control, such as multi-point positioning
Air and Electric Motion: The Best Mix
We have prepared a demo unit that reproduces five processes, including handling,
so that you can actually see how we propose to use both Air and Electric Motion.