Case Study
We introduce Case Studies of the plug-in valve TVG Series in various situations.
CASE1 Small assembling device
ProblemUnexplained stoppages occur in small assembly devices
In the small assembly device, the cycle time is short and the working Component must have a long service life. Accurate operation is required for stable operation, and equipment may experience frequent stops due to valve response delays.
After installationLong service life and improved responsivity, while preventing unexplained stoppages.
The TVG Series is effective for preventing unexplained stoppages, thanks to the improved durability and responsivity of the elastic body seal of 120 million cycles or more. Realizes equipment that never stops and contributes to increased productivity.

CASE2 Beverage Facilities
IssueBeverage facilities have longer and more piping
In beverage facilities, pneumatic valves are often installed in the control panel because water may be splashed, resulting in long and a lot of piping.
After installationWater-exposed environment and compact piping
The TVG Series has a IP65/IP67 (dust-proof, jet-proof) design for tough use in dusty or water-exposed environments. As there is no need to install in the control panel and piping is short, wasteful compressed air can be reduced and responsiveness can be improved.
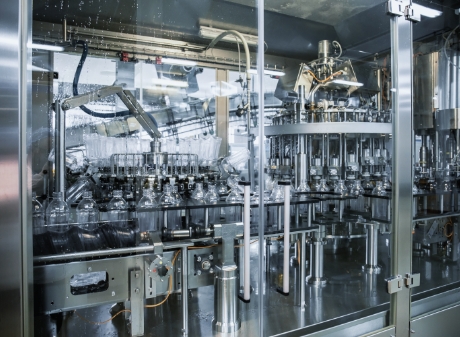
CASE3 Internal pressure explosion-proof panel
ChallengeTo safely use valves without air leaks in explosion-proof areas
Stable operation of the facility is hindered due to air leakage caused by age-related deterioration, etc. There is a danger that the pressure inside the explosion-proof panel will rise as the air leakage from the valve fills the explosion-proof panel.
After installationLess air leakage and stable operation of equipment
The TVG Series provides thorough measures in areas prone to air leakage. With less air leakage, the effect of pressure control inside the board is minimized, contributing to stable operation of equipment.
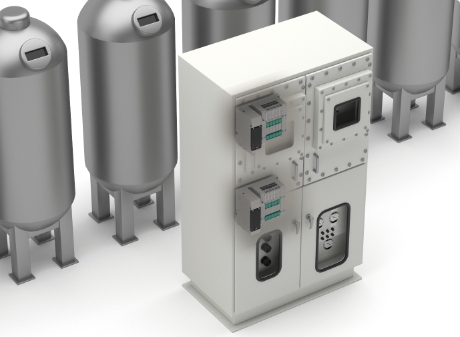
Supports continuous energization
Energy-saving coil (0.1 W) is available as an option to support continuous energization, which is often required for air-operated control.
Special resin
The special resin available as standard suppresses secular change and air leakage from the valve for long periods.
CASE4
Assembly/Inspection
(rotary table)
IssueIt is difficult to install a solenoid valve manifold on a rotary table.
It is difficult to install a solenoid valve manifold on a rotary table because of the risk of wires becoming entangled and disconnected. When using a slip ring (rotary contact), the solenoid valve is generally not positioned on the table due to the risk of malfunction caused by noise generation, and so workpiece positioning is generally done with a mechanical jig.
After installationImproved positioning accuracy
IO-Link Wireless-compatible TVG Series can be installed on a rotatary table without entangling the wiring. IO-Link Wireless has a communication error rate of one in a billion, so signals are highly reliable and solenoid valve malfunctions can be prevented. This makes it possible to improve the positioning accuracy of the workpiece.
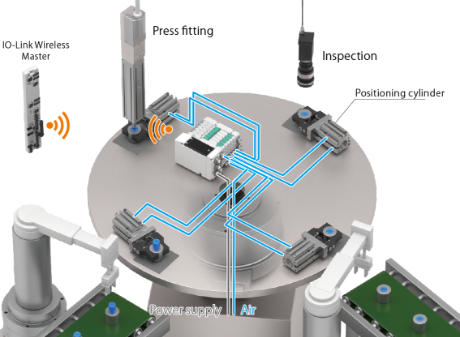
Solenoid valve configuration
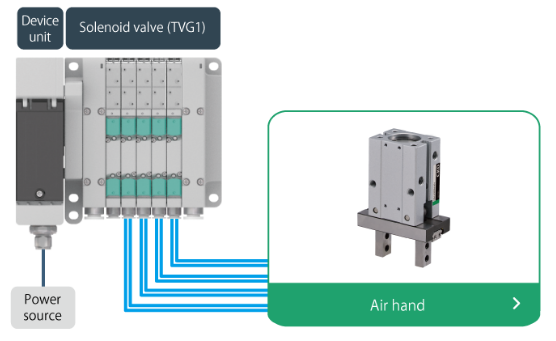
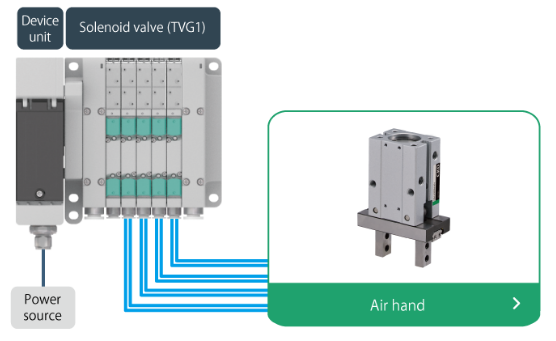
CASE5 Automobile body welding
ChallengeReduce wiring and piping for automobile body welding
In automotive body welding, many components such as cylinders are installed on the jig when parts are transported by robots. Many wiring and piping must be installed with movable measures.
After installationContributes to reduced component installation space and improved wiring layout.
The introduction of the TVG Series and remote IO contributes to reduced wiring of the solenoid valve for cylinder drive and cylinder switch input. Wiring from the PLC is completed with a single Ethernet cable. This contributes to reduction of installation space and improvement of wiring layout for components including IO-Link components.

Remote IO configuration
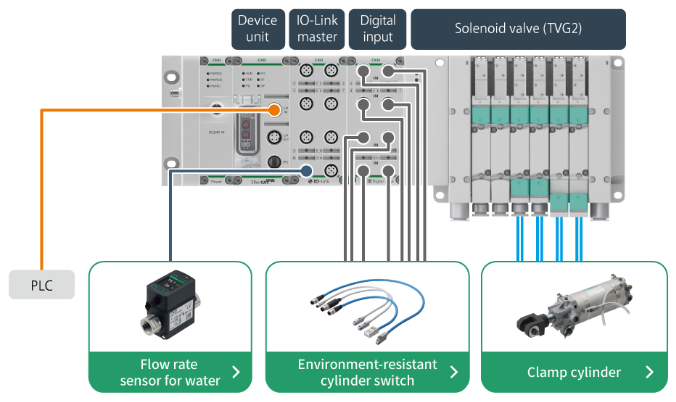
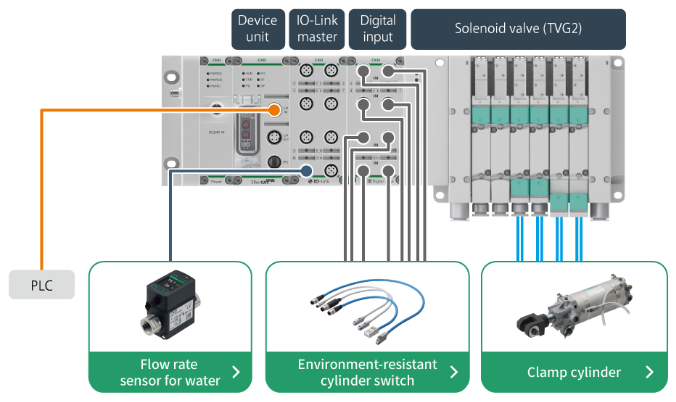