- What is the environment surrounding workers?
- The disadvantages of conventional machines have been eliminated all at once!
- What are the features of the 3rd generation device??
The use of a variety of workers and the practice of reforms in working styles, etc., are important tasks for companies in order to realize a people-friendly work environment and to address labor shortages. In particular, reducing the burden of heavy labor and securing safety are urgent issues. One of the solutions that attracts attention is the creation of a worker-friendly site that utilizes robots, which contributes to the reduction of work load and increased safety. It is said that companies in the automobile and the food industries are quick to set up sites where people are at hand and are continually producing results, which is said to be unprecedented considering the shortage of human resources. With a vision of creating a worksite that is people-friendly, we interviewed CKD staff who provide products that are close to working people and companies, and asked about the latest applications and product trends.
Freely move heavy objects Turn heavy labor into light work with the power of technolog
In factories and construction sites where heavy objects are often handled, more than half of the labor accidents that occur are lower back pain. With such harsh working environments, there are no lasting replacements. Furthermore, in Japan where the declining birthrate and the aging population are progressing, it has become essential to consider all types of workers for a continuous corporate management. However, worksites where heavy labor exist are not meant for everybody.
In order to eliminate the chronic human resource problems that the Japanese industry faces, there is a movement to promote automation of production lines using industrial robots and the like. However, in the production process, there will always be sections that cannot be automated but rely on manpower. Such heavy labor often becomes a bottleneck that hinders the improvement of line productivity.
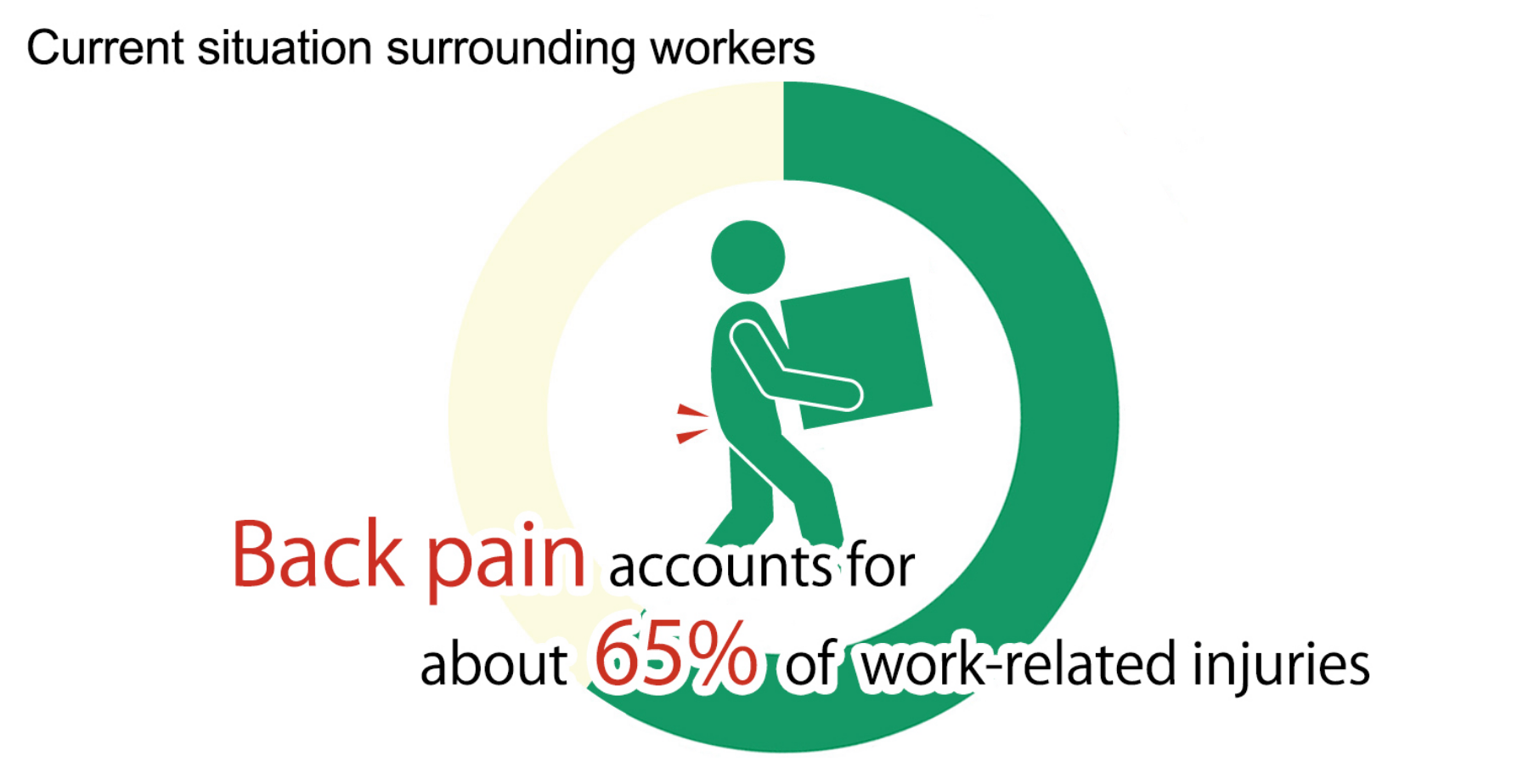
Reducing the burden of heavy labor is an indispensable task to improve the productivity of the entire line and the working environment of workers. Among companies looking for solutions to these problems, what has attracted a lot of attention is “Human Assist Products” that assist workers with the power of machines, turning heavy labor into lighter tasks.
- What is the environment surrounding workers?
- The disadvantages of conventional machines have been eliminated all at once!
- What are the features of the 3rd generation device??
Reducing various heavy labor with the following approach.
To date, there have been several types of human assist products, such as belts, arms, and powered suits, which are intended for use in factories and the like. However, there are drawbacks to the commonly used ones, such as difficulty in operation and the limitation of utilization because of the need for large installation spaces.
CKD's "PowerArm PAW Series" solves such issues in an instant. The most important feature of the PowerArm is that it adopts a structure that supports and reduces the weight of the load from below. By joining up to three arms and incorporating a weight-supporting mechanism, it has become possible to secure a wide range of movement, and to freely handle vertical and horizontal motion.
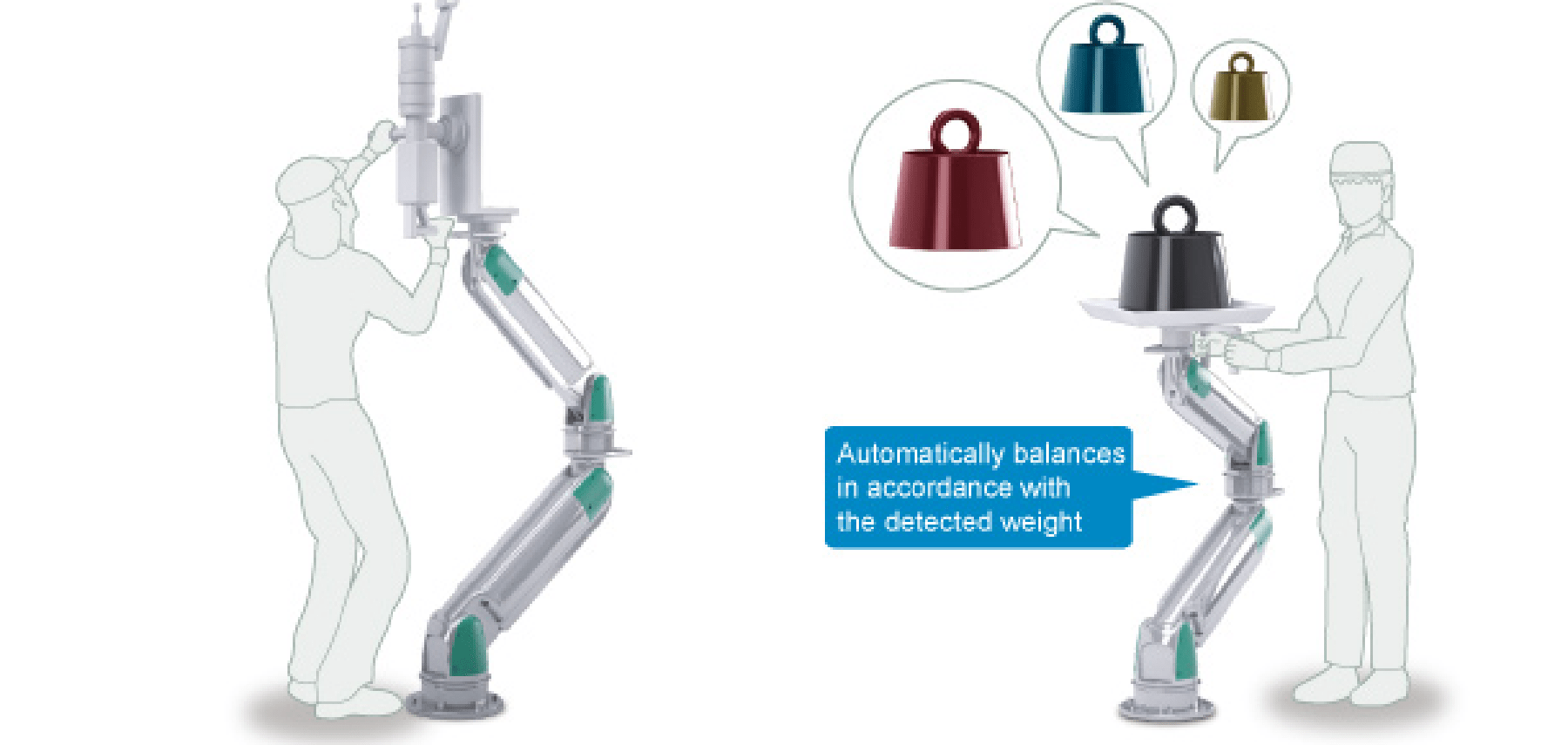
It is possible to maintain the weight of jigs and tools in a balanced state, and to handle workpieces of different weights.
In the field where heavy goods are handled, there are many tasks that cannot be handled without supporting the weight from below. A typical example is the work of incorporating a heavy engine from under the vehicle body in a car production line. With the powerful arm, you can handle these tasks without any difficulty. Of course, it is also possible to support the objects from the top using jigs such as hooks, vacuums and clamps. In addition, it can be installed and used in a narrow spaces because it can be stored by folding the arms with little interference with surrounding objects. The PowerArm may be the definitive version of the power assist products with a very wide range of applications.
The roots of the PowerArm is found in the power assist device developed by Nissan Motors in 2008. It was based on the technology of incorporating a pneumatic cylinder developed by the Tokyo Institute of Technology into the interior of the arm. CKD contributed to its development by providing a cylinder that minimizes the sliding resistance (mechanical resistance of the moving surfaces where the parts meet). Then, in 2013, CKD acquired a license for its power assist device from Nissan. The product created by CKD with its own improvements is the resultant PowerArm. The first generation of the production version of the PowerArm was launched in 2014. Now, Nissan Motors has incorporated the PowerArm into their factories.
The PowerArm assists the operator with a mechanism called "automatic operation pressure regulation control". The load sensor detects the weight of the object to be supported and the acceleration due to the movement of the worker with a load sensor, and proportionally controls the air pressure according to the change in load using CKD's highly accurate electro-pneumatic regulator. Since the load and the load generated by the movement and the pneumatic cylinder output inside the arm are always balanced, it is possible to flexibly cope with the transfer of workpieces of different weights. CKD produces many parts that make up the PowerArm internally, and by combining them in a highly optimal manner, we have succeeded in creating a human assist product that the operator can treat like an extension of his or her hands and feet.
- What is the environment surrounding workers?
- The disadvantages of conventional machines have been eliminated all at once!
- What are the features of the 3rd generation device??
Naturally blends in with the workplace A safe and unintimidating design.
CKD demonstrated the 3rd generation PowerArm released in January 2019 at the 5th [Nagoya] Mechanical Components & Materials Technology Expo (held from 17 to 19 April, 2019). Our booth where an actual machine was exhibited, attracted the attention of countless of visitors.
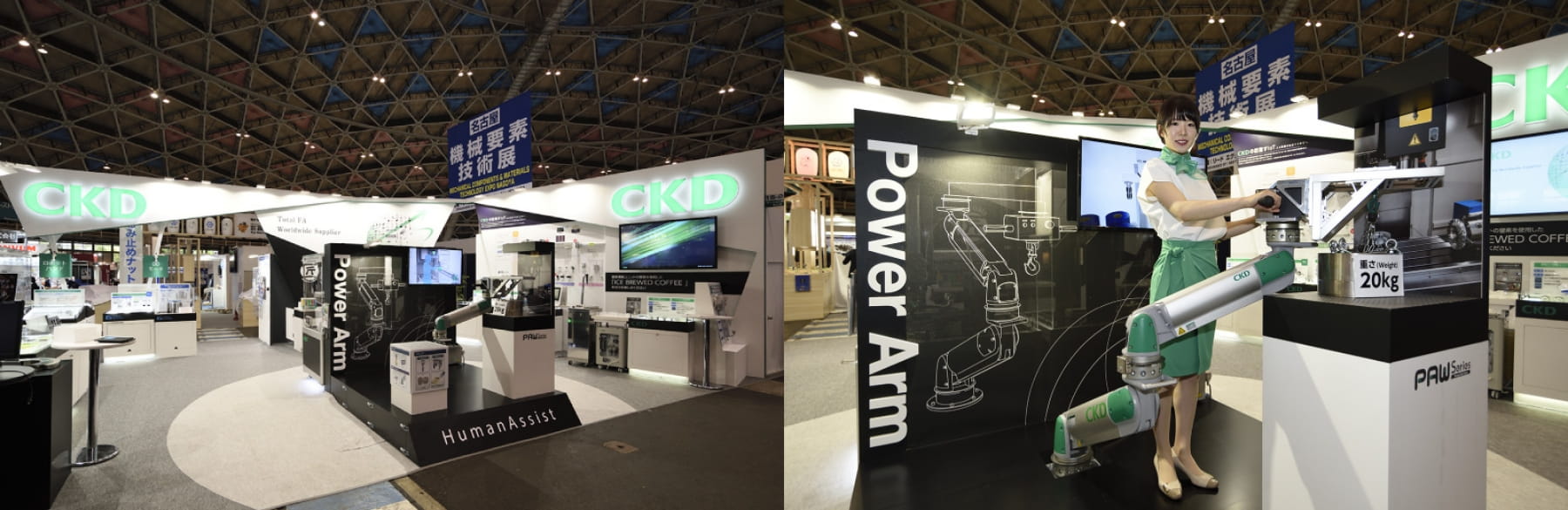
(Right) The PowerArm PAW Series has a compact, round and comfortable design.
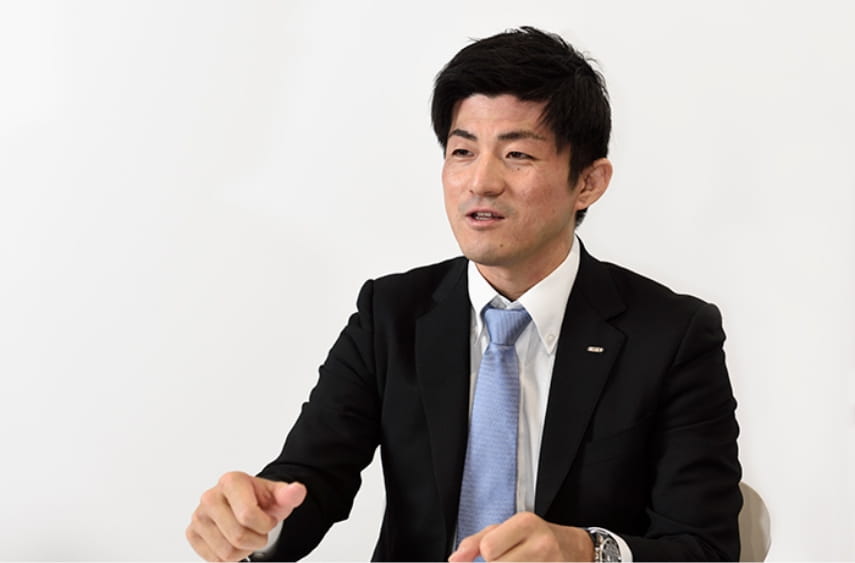
CKD Corporation
Development Group, Motion & HA Business Development Department
Group Leader
Mr. Satoshi Wakasugi
"The 3rd-generation device made use of all the comments received from the first two generation users to carefully consider what was required when working with people and thoroughly improve safety and usability," commented Mr. Satoshi Wakasugi, leader of engineering group in CKD FA system BU, HA Business Development, who developed the PowerArm.
The PowerArm, which is an assistance machine, should not harm people by any means. Therefore, in the third generation unit, the gap between the arm joint where fingers could find their way in and get pinched was eliminated. Moreover, curved surfaces which are safe for human contact are used for the entire external body.
In addition, functional safety during a sudden occurrence was also incorporated. For example, when carrying heavy loads, the arm will prevent them from dropping even if the air source is cut off. This technology relies on a block valve which closes the valve controlling the compressed air passing in/out to the cylinder. It stops the movement of the cylinder that is supporting the load. The same safety function works even when the power is turned OFF. Furthermore, it is possible to maintain the position at the time of emergency stop by attaching an optional rotation lock (normally closed type).
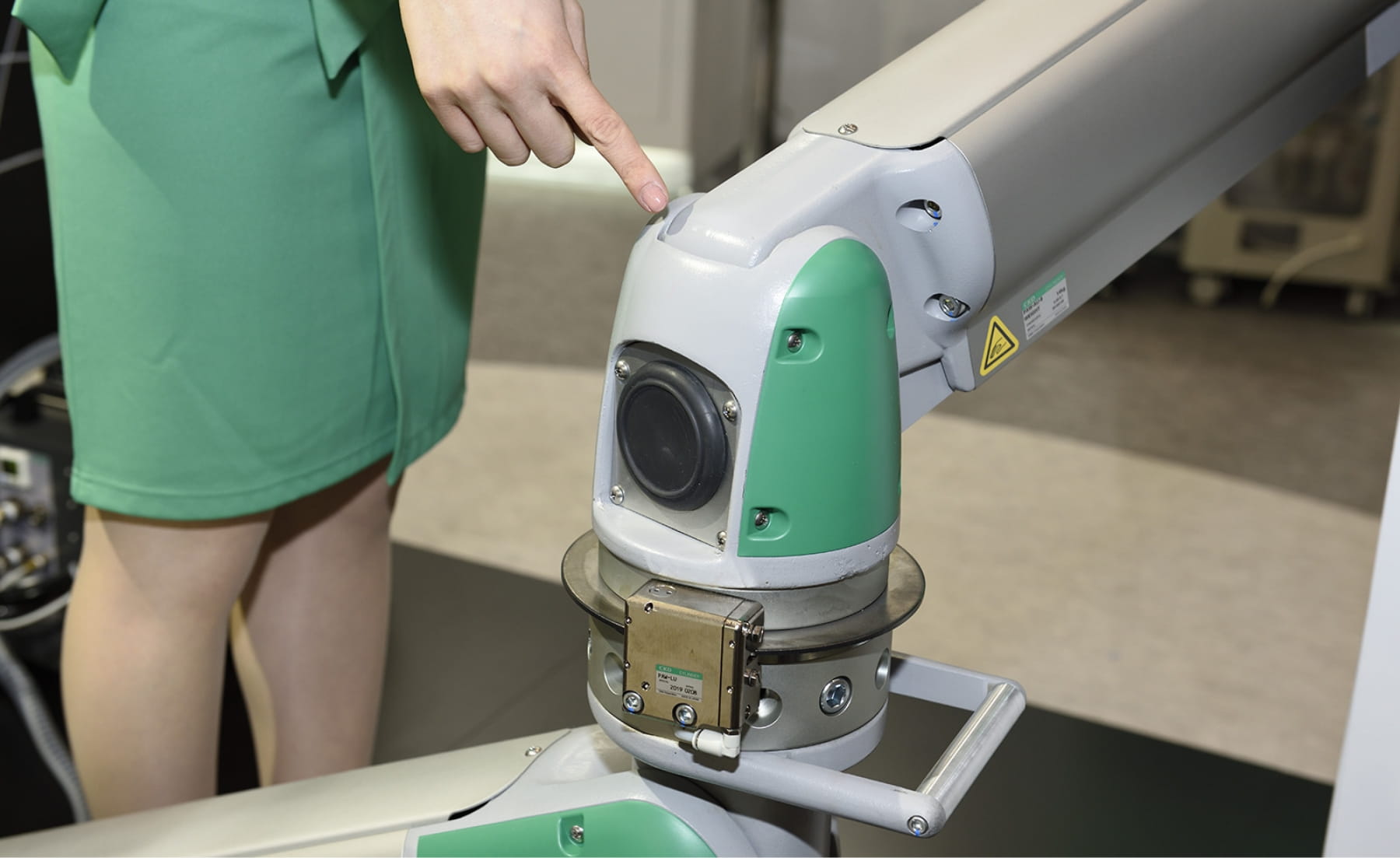
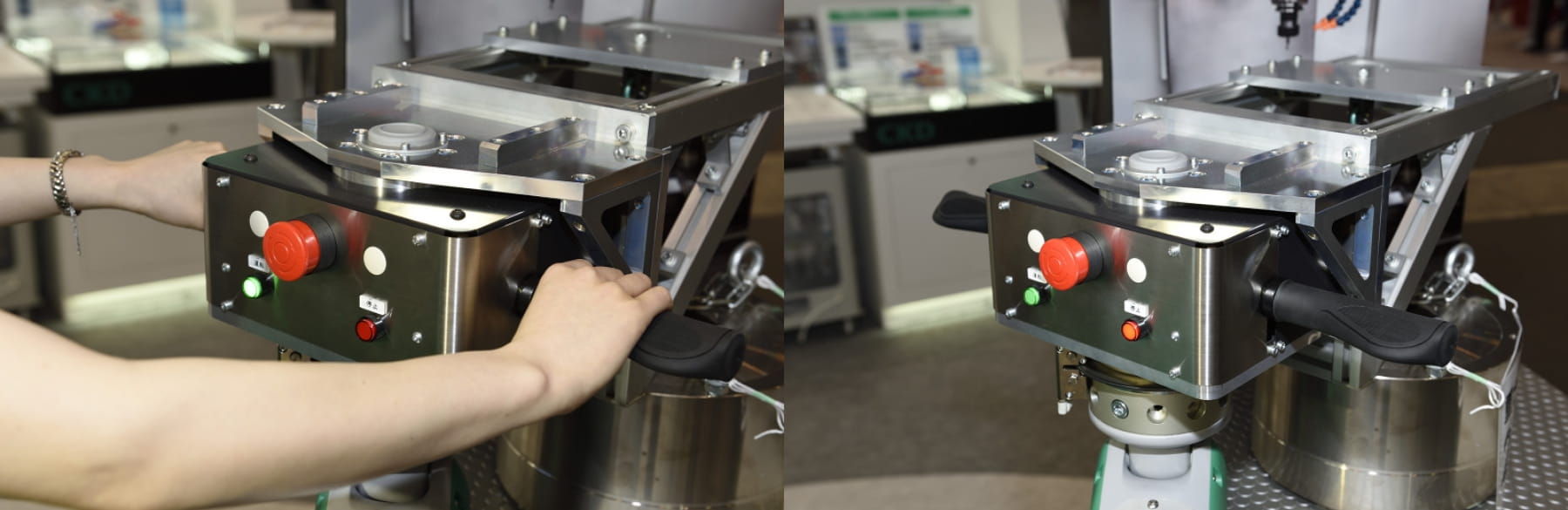
(Right) The stop lamp comes on when the handle is released
The first thing that surprises people with the 3rd generation unit is that the look is so sophisticated. Even though it is a powerful machine that supports human power, it has a soft impression to it. "The third-generation unit has been designed with a refined image from the beginning of development while we were analyzing its rigidity and functions," said Mr. Wakasugi.
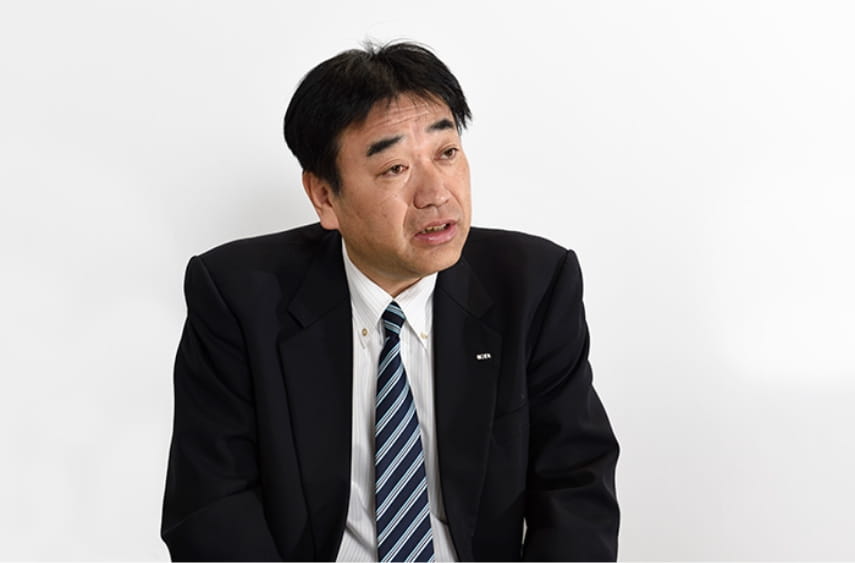
CKD Corporation
Motion & HA Business Development Department
General Manager
Mr. Koichi Sato
With industrial equipment, function and performance are the top priorities, and some people may think that the appearance is not required. Certainly function and performance are important, but that is not enough for machines that work together with people. A machine that gives a sense of incongruity or intimidation by just being close to it, adversely affects the efficiency of the worker. Industrial machines of the future must coexist with all workers in the factory, and be close to nature. A good appearance is no longer an option, but an important feature to build into all devices. In the field of consumer electronics such as home appliances and smartphones, manufacturers are increasingly promoting designs in ways that will incorporate designs that users feel comfortable and easy to use. However, in order to put it into practice, a high level of technical ability is necessary to implement the necessary functions in a compact manner without degrading the performance. It is only with CKD's advanced components and packaging technologies that allow industrial equipment to pursue its appearance.
In addition, it is easy for customers to maintain the arm as it has a structure that can be easily disassembled much like building blocks. In the third generation unit, one would start from the top and remove four bolts in each axis. Also, a paid maintenance service will be offered in the future. "The PowerArm is an indispensable device for the customer's workplace. We wanted to create a safe and long-lasting environment," said Mr. Sato, General Manager of the HA Sales Dept., Sales Division.
Expand the worker's ability with "human-machine integration"
Boost productivity in the field
Particularly popular are the assembly lines of engine parts and EV motors in the automotive industry. It is also gaining momentum in replacement work of jigs and parts of machine tools performed in an akward position in narrow spaces, as well as for the transport of heavy cardboard. In addition, there are many examples of use in the food industry where heavy labor remains in such operations as loading and unloading packaging roll materials from pallets and installing them into packaging machines.
There are many companies doing heavy work in narrow spaces, which cannot be accomplished without using the PowerArm. "We have been happy to hear customers say that they can no longer work without this device." (Mr. Wakasugi) Furthermore, there are testimonies where a two-person job is now possible with just one worker, and others where a much heavier payload is now possible, surpassing the worker's physical limitations." (Mr Sato).
CKD proposes to use the PowerArm not only for human assistance but also for mechanical assistance. For example, a robotic arm that can only lift a 10 kg workpiece can move as much as 30 kg if the PowerArm is used in tandem. Making a robotic arm handle heavy work is no small feat as a higher capacity robot easily becomes extremely expensive. The PowerArm can be used to construct a cost-effective delivery system.
Although the device is currently being introduced to factories equipped with compressed air systems, it can also be used at construction sites, etc., by providing a compact compressed air supply unit. "In the future, we will also consider introducing an all electric unit" (Mr. Sato), and we can expect an evolution that will further expand the applications.
There are three types of arms (at 0.5 MPa pressure) for the 3rd generation device: the model with an inner diameter of 80 mm with a 30 kg payload (the sum of the weight of the work and the attachment), the model with an inner diameter of 100 mm with a 50 kg payload, and a 125 mm model with an 80 kg payload. It can be freely selected according to the work to be handled. When combining and using multiple axes, assemble in order from the largest inner diameter tube model. For example, in the case of using three axes, the 125 mm model will be mounted on a fixed anchor or a carriage as the base, then the 100 mm will go on top, and finally the 80 mm will be sequentially stacked. As a result, a wide operating range of 1750 mm vertically and 2100 mm horizontally can be secured.
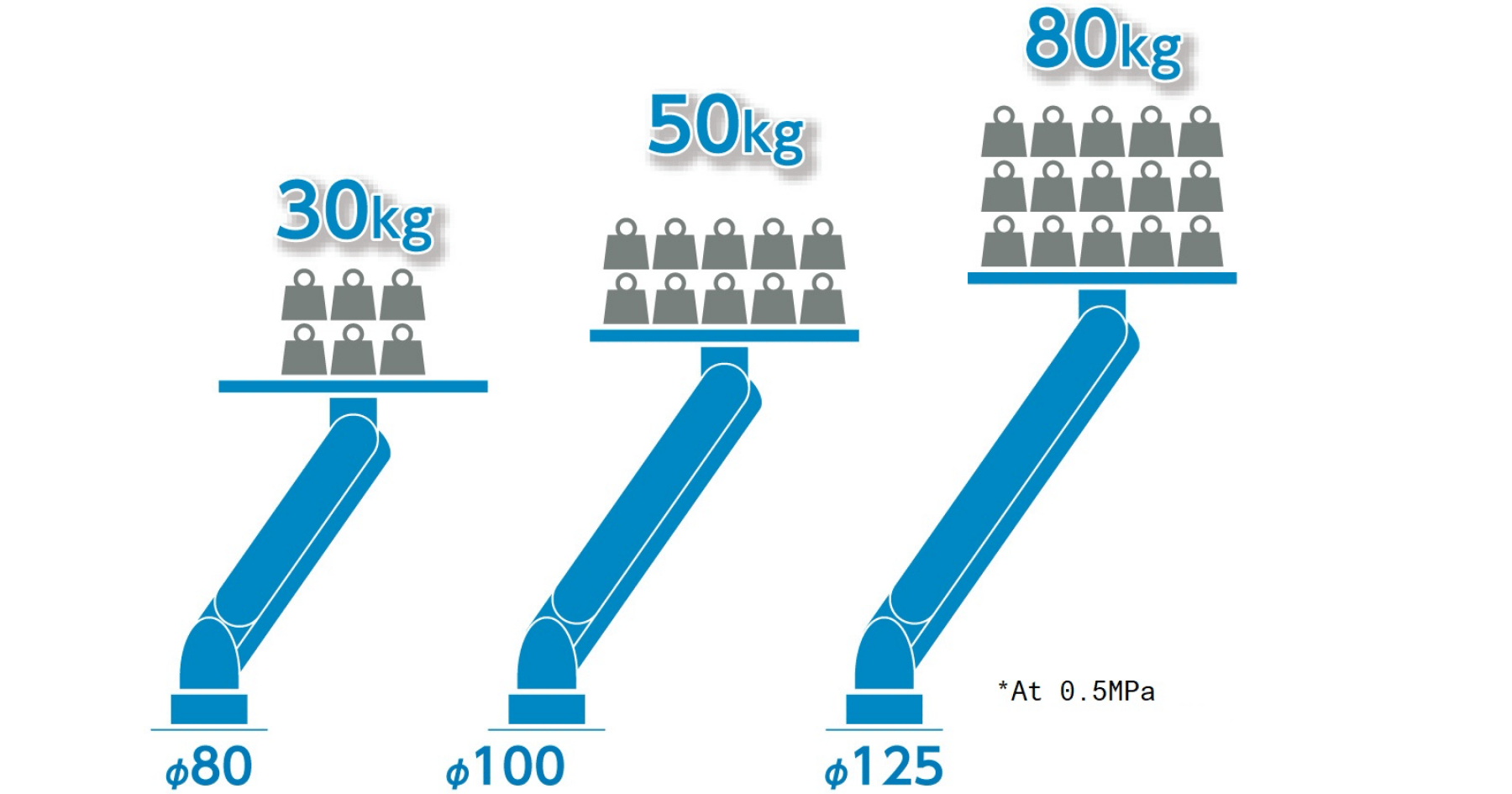
The attachment of the part that supports the workpiece is custom developed according to the work to be handled and the application. "We will create from scratch, attachments with the optimal shape and function, which will not drop the work being transported, yet it will easily attach and detach the work," (Sato). For example, a hook for suspension is used when transporting an engine block for an automobile, a suction attachment is used when handling bags of material or a plate-like material such as glass in food factories. An inner diameter clamp will be prepared to support the core portion when transporting roll materials, and an outer clamp when carrying round objects, container boxes, etc. At CKD's Komaki Factory, we will test using the actual work that will be transported, and proceed with development. Assembly and removal of the attachment to the arm is extremely easy. If the arm is moved to another location by a carriage and the attachment is replaced for the new application, it will be possible to share the arm in multiple scenes.
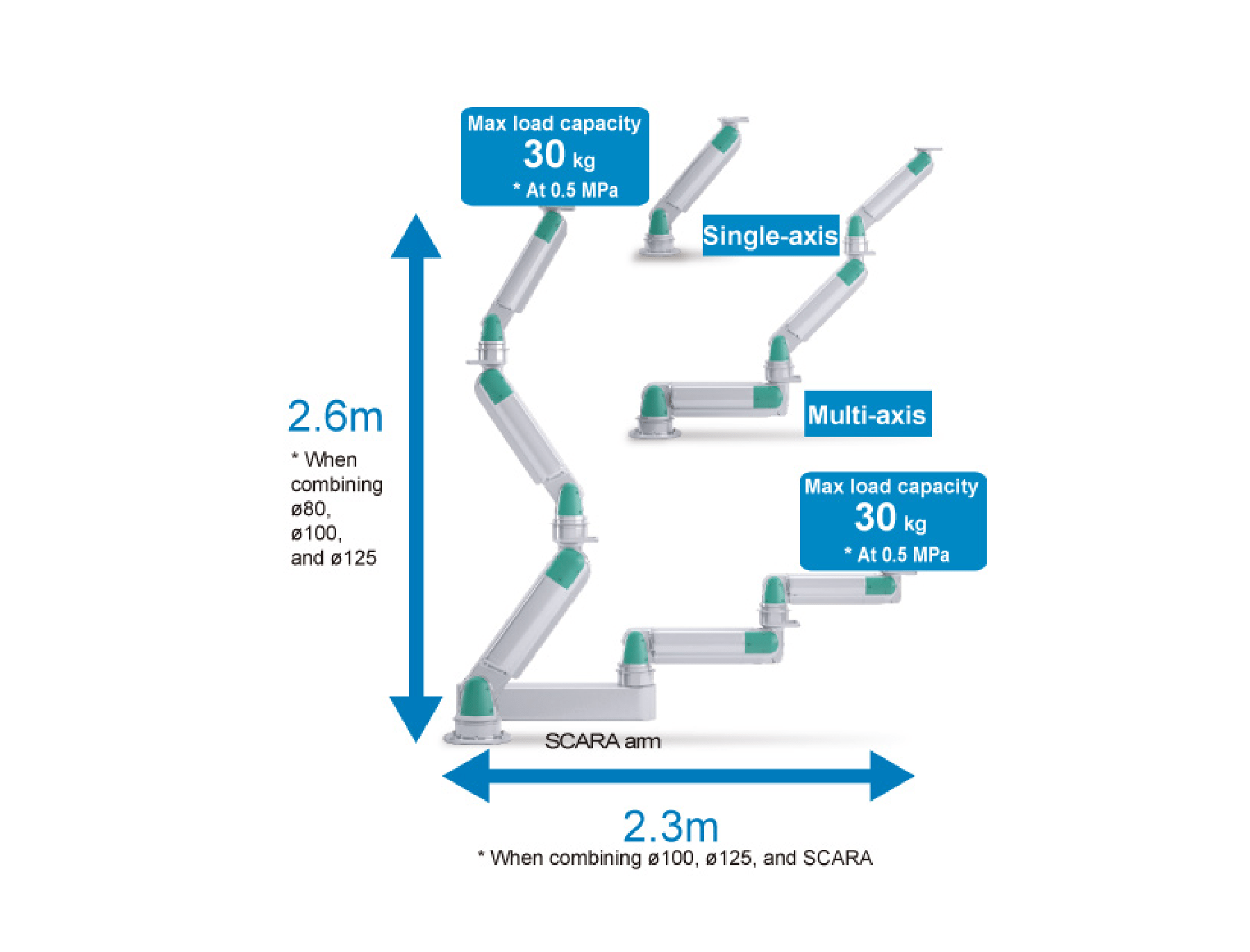
CKD can deploy demonstration machines to sales bases throughout the nation and bring them to customers for demonstrations. In addition, the need to reduce heavy labor is expected to increase overseas. It has already been introduced in China, and CKD plans to establish a platform to provide sales and services for future global expansion. The PowerArm has already acquired the European safety standard CE marking, and can be sold in the European market. The future of releasing workers all over the world from heavy labor is now at hand.en introduced in China, and CKD plans to establish a platform to provide sales and services for future global expansion. The PowerArm has already acquired the European safety standard CE marking, and can be sold in the European market. The future of releasing workers all over the world from heavy labor is now at hand.
*The content of the above excerpt have been re-edited from Nikkei xTECH advertisement (first appearance: May 15, 2019) with permission of Nikkei BP. All rights reserved (C) Nikkei BP