"Air Sequence Circuit" and "Double Safety Circuit" Assist Work in Explosion-Proof Areas
Material maker A
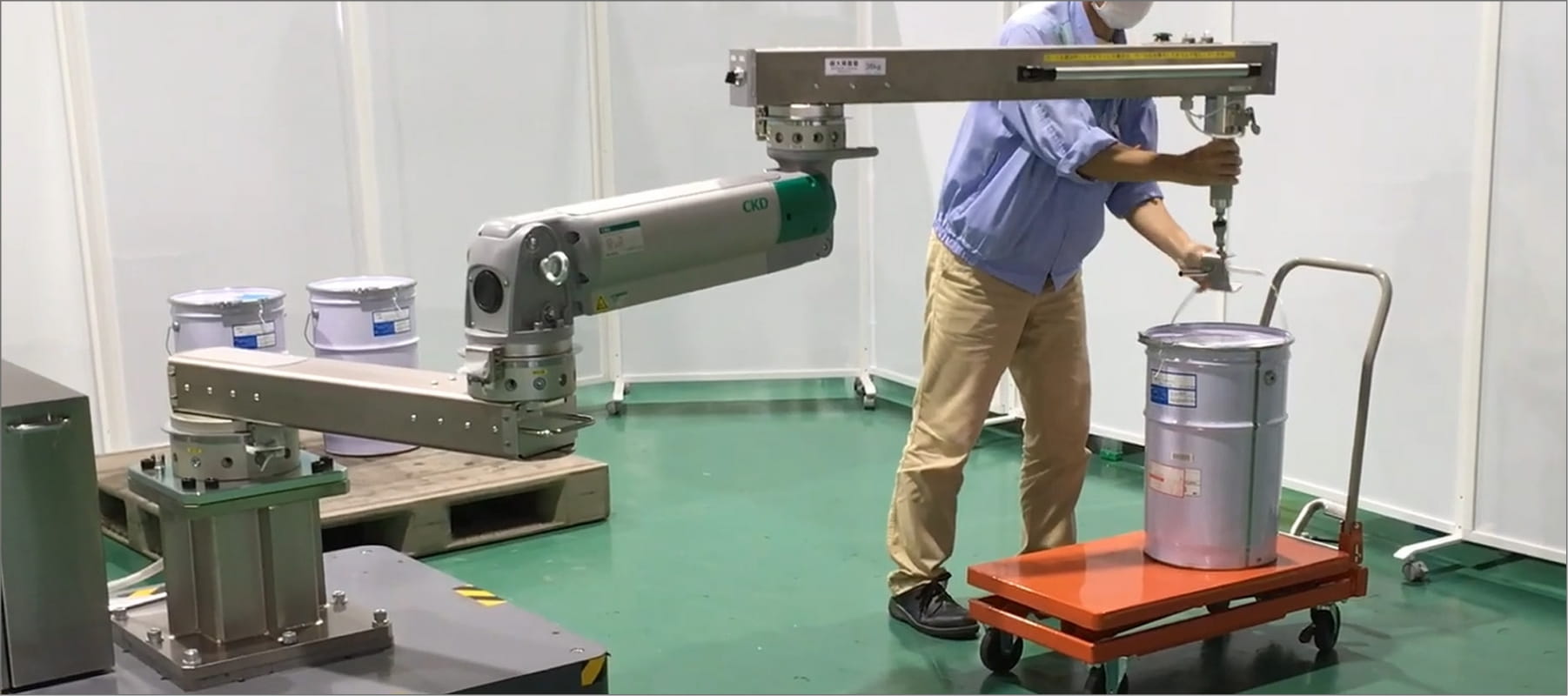
Here is an example of improvement of pail (25kg) transportation in an explosion-proof area and in a narrow space with a low ceiling at a material manufacturer A Co.
Problems
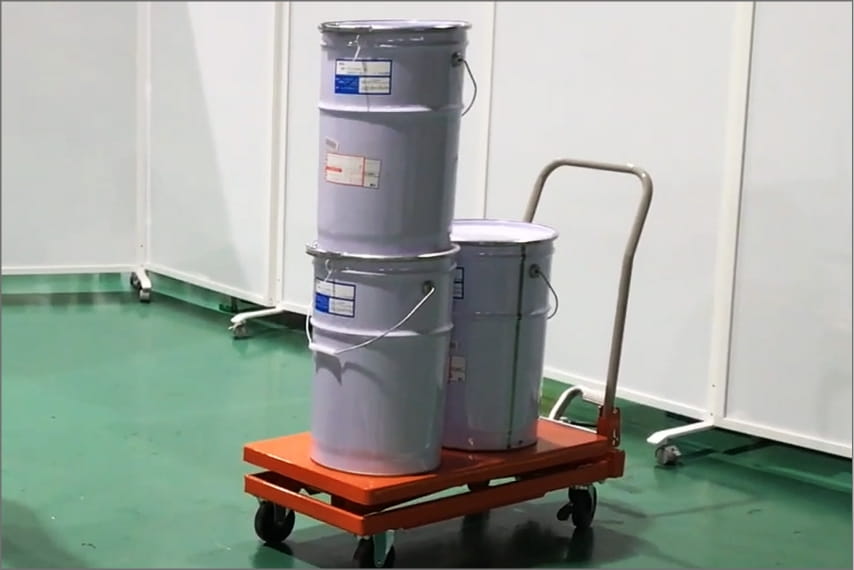
Transporting heavy objects in explosion-proof areas
Manually transporting pails (25 kg) in the low-ceiling explosion-proof area.
The pail handles were so thin that they were hurting the operator's hands when transferring the pail, and the operator was suffering from lower back pain caused by working in an awkward posture.
However, as the ceiling was low and it was not possible to use assistance devices from the top, common arm-type balancers and electric winding balancers were not available. However, the ceiling was too low to use assistive devices mounted on the ceiling, so a common arm balancer or an electric hoisting balancer could not be used.
We were looking for an assistive device that could be used in explosion-proof areas with low ceilings.
Reasons for Adoption
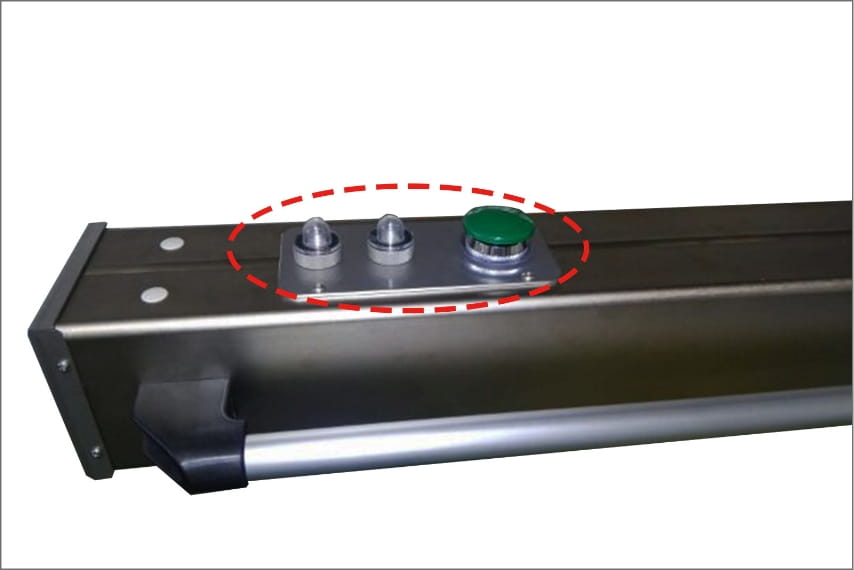
Safe and Reliable Equipment for Explosion-Proof Areas
CKD's PowerArm uses an "air sequence circuit" that is controlled only by air, not electricity. Safe to use even in explosion-proof areas. The "limit switch" is turned ON when lifting, and a double detection is performed by pressing a button. Safety is enhanced by two types of switches: a limit switch that operates when a workpiece is suspended, and a button pressed by the operator. If the button is pressed but the workpiece is not suspended, the arm will not move unexpectedly and can be used safely. Another deciding factor in the adoption of this device was that it can be used even with low ceilings because it is mounted on the floor with a bottom-up motion.
Effects post introduction
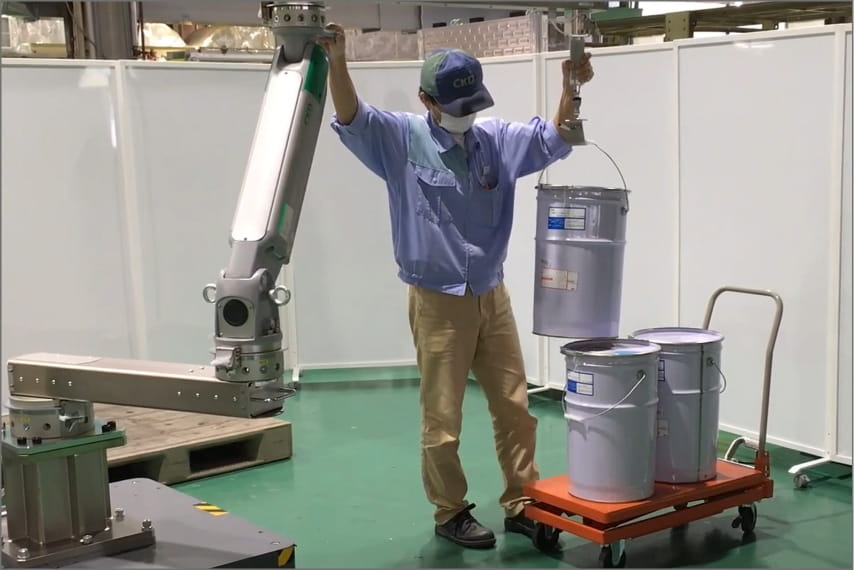
Safe and Secure Transfer of Work for Everyone
The introduction of the assistive device in the explosion-proof area has eliminated the need for manual transfer, and has also eliminated hand-strain during work.
Lower back pain caused by working in an awkward posture is no longer a problem, and anyone can work on the task, not just certain workers.
A double safety circuit prevents the arm from moving up without the workpiece, even if the switch is accidentally pressed, allowing the operator to use the product safely and without injury.